Custom Glass Bottle Manufacturers
As the best custom glass bottle manufacturers,Crystal Glass packaging assists customers in making unique glass bottles starting from the first step of custom made bottles, providing technical feasibility and solutions in shape design and bottle labels.Meanwhile we can provide glass bottle manufacturing process,such as,custom printed glass bottles,custom embossed glass bottles,hot Stamping,Carving,Frosted bottle,Carving...
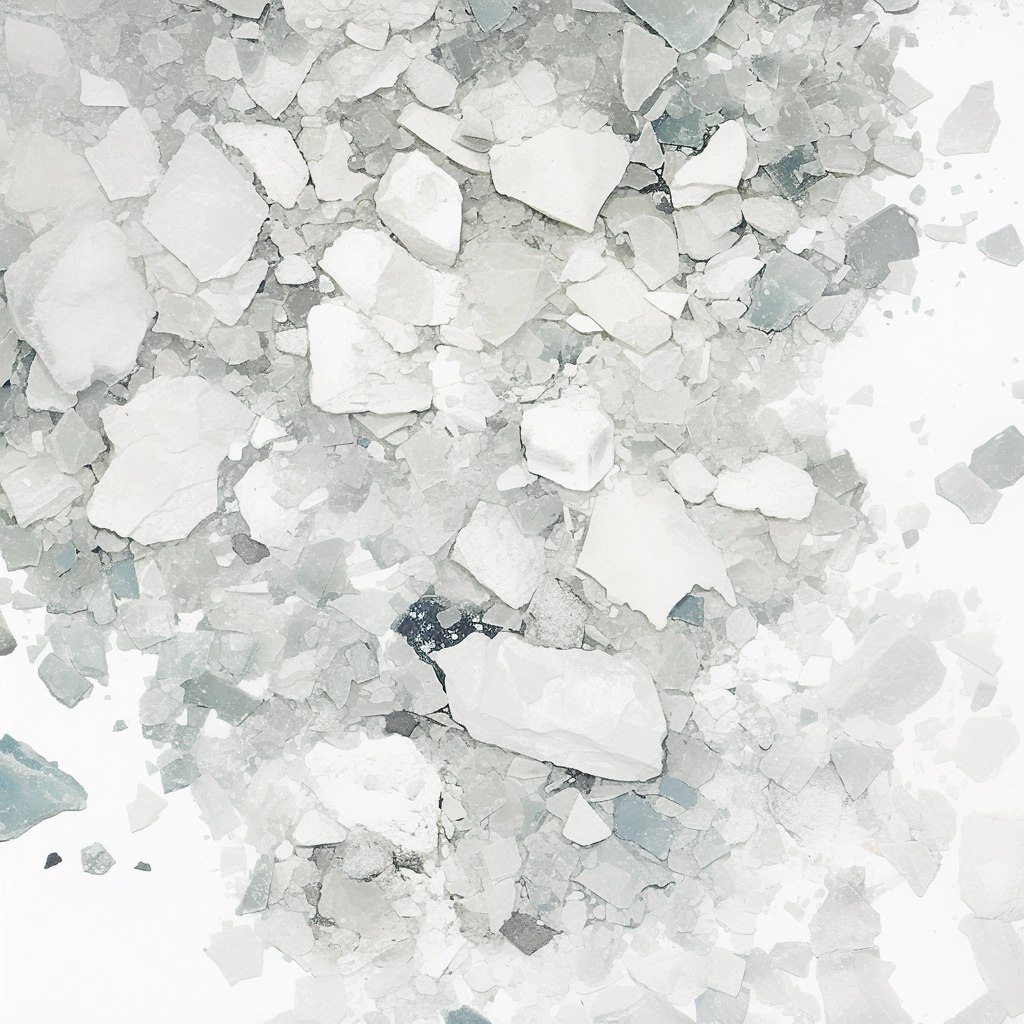
-
01
Silk Screen Printing -
02
Hot Stamping -
03
Decal -
04
Frosting -
05
Coating -
06
Carving -
07
Label -
08
Electroplate -
09
Closures
Watch the Video
Screen printing is a printing method that transfers ink to the surface of glass bottles through the mesh on the screen printing plate. First, make a screen printing plate, usually a screen made of nylon, polyester and other materials, apply photosensitive glue on it, and make a printing plate with a specific pattern through exposure, development and other processes.During the printing process, place the glass bottle in a suitable position and fix the printing plate at a certain height. Then, pour the prepared ink on the printing plate, and use a rubber scraper to scrape the surface of the printing plate at a certain angle and pressure, so that the ink is evenly transferred to the glass bottle through the mesh.
Watch the Video
First, make sure the surface of the glass bottle is clean, dry, free of oil and impurities to ensure the quality of the hot stamping effect. Choosing the right hot stamping film is also a key step. Hot stamping films are available in a variety of colors and patterns to meet different design needs.
Next is the hot stamping process. Place the hot stamping film on the part of the glass bottle that needs to be decorated, and heat the hot stamping film through a heating device. Usually a hot stamping machine is used, which can accurately control the temperature and pressure. Under the appropriate temperature and pressure, the metal layer on the hot stamping film will melt and adhere to the surface of the glass bottle, forming a distinct and lasting hot stamping pattern or text.
Watch the Video
Design the pattern according to customer needs, and then print the designed pattern on special decal paper. Decal paper usually consists of base paper, ink layer and protective layer.
Cut the decal paper into suitable size and shape to fit the size of the glass bottle and the decal location. Soak the cut decal paper in water to separate the decal paper from the base paper. This process requires mastering the soaking time and water temperature to ensure that the decal paper can be separated smoothly without damaging the pattern. : Take out the separated decal paper from the water and gently stick it to the predetermined position of the glass bottle. Use tools such as rubber scrapers or sponges to gently squeeze the decal paper to expel the air and moisture between the decal paper and the glass bottle to ensure that the decal paper fits tightly to the surface of the glass bottle.
Wash the glass bottle thoroughly with water or detergent to remove dust and dirt on the surface, and then dry it. Mix frosting powder and acid according to a certain ratio, stir evenly to make frosting liquid. Apply the frosting material evenly on the surface of the glass bottle by soaking, spraying or brushing. When soaking, immerse the glass bottle completely in the frosting liquid and take it out after a certain period of time; when spraying, use a spray gun to spray the frosting liquid evenly on the surface of the glass bottle; brushing is to use a brush to apply the frosting paste on the glass bottle.
Watch the Video
Choose the right paint based on the required color, gloss, durability, etc. Common paints include baking varnish, UV paint, water-based paint, etc. Spray a layer of primer on the surface of the glass bottle to enhance the adhesion of the paint. Control the thickness and uniformity of the primer to avoid problems such as sagging and leaking. According to the design requirements, choose the right color and topcoat for spraying. Control the distance, angle and movement speed of the spray gun to ensure that the topcoat is evenly covered on the surface of the glass bottle. Multiple spraying can be performed to achieve the desired color depth and gloss.
Laser engraving uses a high-energy-density laser beam to illuminate the surface of a glass bottle, causing the glass material to vaporize, melt, or change color instantly, thereby forming the desired pattern, text, or texture on the glass bottle. Laser engraving has the advantages of high precision, high speed, and non-contact processing, and can achieve fine engraving of complex patterns without causing mechanical damage to the glass bottle.
Watch the Video
Arrange the glass bottles neatly on the feeding conveyor belt of the labeling machine, and convey the glass bottles to the labeling station through the conveyor belt. The self-adhesive label is usually wound on the label reel. The labeling machine pulls the label from the reel through a traction device, and passes through a series of guiding and tensioning devices to keep the label in a flat and stable conveying state. When the glass bottle arrives at the labeling station, the labeling head of the labeling machine will peel the label from the base paper and accurately stick it on the surface of the glass bottle.
After the label is attached to the glass bottle, the labeling machine is usually equipped with a smoothing device, such as a roller or a scraper, to smooth the label, eliminate the bubbles between the label and the glass bottle, and make the label stick to the glass bottle more evenly.
Watch the Video
The glass bottle electroplating process usually consists of cleaning, conductive layer coating, and electroplating. The glass bottle coated with a conductive layer is placed in an electrolytic cell and connected to the cathode of the power supply (as the negative electrode of electroplating), and the anode usually uses a metal plate (such as a chromium plate, a nickel plate, etc.). During the power-on process, the metal ions in the electroplating solution will move to the cathode under the action of the electric field and be reduced to metal deposition on the conductive coating of the glass bottle to form a plating layer.
We offer a wide variety closure caps and corks. Screw caps, aluminum caps, wooden corks, polymer corks, with Logo designs, carve, silk screen, laser engraving and etc.
Many manufacturers of glass bottles and jars receive a variety of product quality problems from customers after they leave the factory, causing customers to complain and causing losses to both parties. The main reason is the improper quality control during the production process. Therefore, in order to ensure the quality of glass bottles and jars, manufacturing enterprises should do the following: